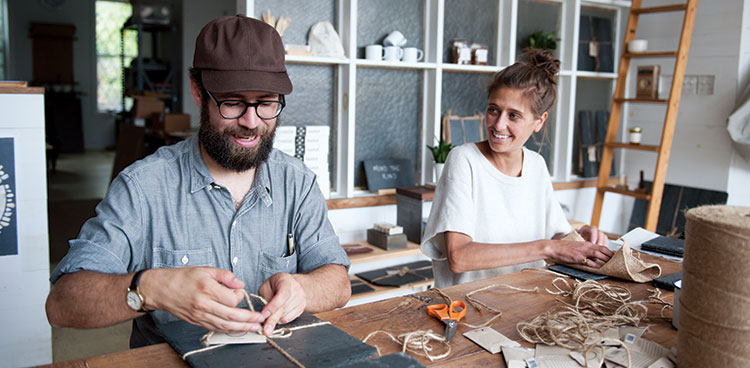

Even in the quarry, slate has natural stratification that makes it good for chiseling into flat pieces.

Large pieces of slate are loaded onto the conveyor belt from a backhoe outside, then are cut down into more manageable pieces with a block saw.

After cutting the chunks of slate are more manageable in size, but still don’t resemble the final product.

Bill Hadeka, father of Brooklyn Slate Company co-founder Kristy Hadeka, hand splits slate into thin pieces with a chisel and hammer.

Using a trimming machine, the edges of the slate are trimmed to a textured bevel; this is where the final size of the slate takes form.

Each slate is hand-polished with food grade mineral oil. Tice and Hadeka recommend repeating this process a couple of times a year to keep slates looking their best.

Brooklyn Slate Company co-founders Sean Tice and Kristy Hadeka package slates with twine, a soapstone pencil, and care instructions in their Brooklyn, New York store.